——2020-2021 Development Review of Electronic Control Workshop
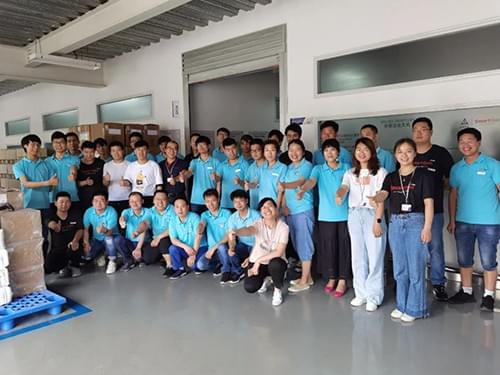
Fast forward to 2021, when writing this article, it is the time for electronic control workshop to work orderly and make capacity improvement at full steam. Looking at the focused eyes of the staffs while working and the continuous products output on the newly added production line, I involuntarily think back to the previous time.
Once upon a time, the electronic control workshop in the production center was troubled by the few orders, poor efficiency, and production quality was controlled by manual inspection. The development of the whole department seems to have encountered a bottleneck, which is incompatible with the situation of the company’s frequent success reports. The director scratched his head and staffs were demoralized. What should we do to solve the difficulty?
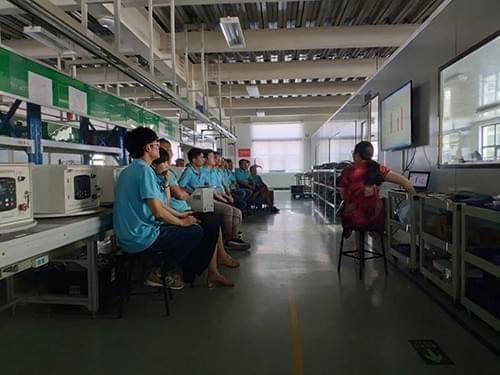
At the beginning of 2020, department leaders and workshop staffs gathered together to list the current situation of the workshop one by one, making everyone deeply aware that “Unless change, otherwise a dead end!” Change started with the director. The director changed the concept, adjusted the leaders and clarified the rules and direction of production management in the workshop. What ignited was the passion of all leaders and staffs, what broke through was the barrier of inertial thinking. Soon, the efficiency was improved, the orders from big customers came in droves, the staff turnover rate was also dropped dramatically, and the workshop soul was created.
Be prepared for crisis is necessary for us. A moment of success is important, but if you want to be excellent all the time, you have to constantly summarize and improve, and firmly grasp the pulse of the workshop progress. Therefore, the main purpose of this article is to review past year and summarize the good experience.
Firstly, cultivate a strong team with people as the core. The company leaders often hire external elites and internal backbones for management knowledge, management methods and other trainings. In various trainings, the electronic control workshop gradually and systematically understands the core of workshop management and gradually practice it, which has also achieved good results.
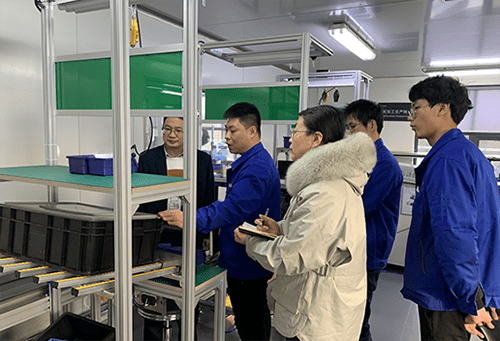
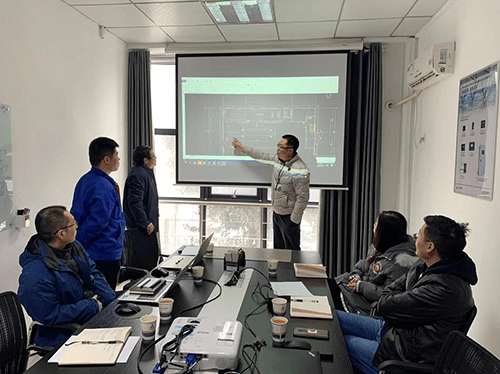
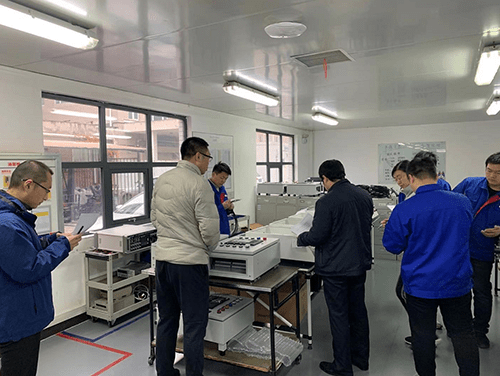
The workshop constantly makes efforts to cultivate management backbone, technical backbone, and technical experts, to activate the working atmosphere of the staff, to enhance the enthusiasm of the staff, and to conduct technical competitions and production skills assessment regularly. We hold various recreational activities such as table tennis, badminton competitions, chess game, performance during break time.
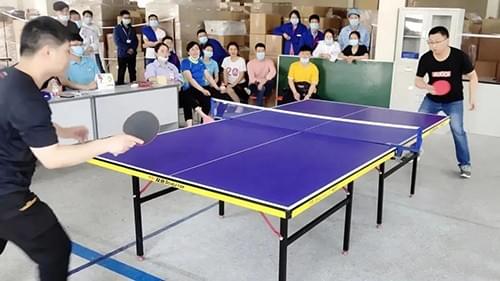
Then, hold high the banner of “continuous improvement”, and continue to transform and optimize the production line with a focus on efficiency:
The daily delivery capacity of HT22M series small heaters can reach 50 sets at most. After many initial tests of one stream production mode, simulated operation, and the joint efforts of equipment and process department, electronic control workshop, and R&D center, the small heater has added an automatic belt production line. After several operations, line balance adjustment and other optimization and transformation, the daily delivery capacity has reached 150 sets. At the same time, the dry air tightness test transformation is being carried out on the line, and the daily delivery capacity of 200 sets will soon be realized! The operation action decomposition of each process, standardized operation methods, high-precision air tightness test equipment, strict insulation and voltage withstand test standard for testing, ensure the production of high-quality small heaters.

The orders of marine machine production line are mostly tailored for customers, “private customization” with high-quality lean production. But in order to improve the delivery capacity, equipment and process department and workshop also make a series of improvements. Specially designed L-shaped production line for marine machine, SOP, tools and materials are placed nearby. The production cycle of marine machine products is greatly shortened by designing the wiring line length in advance, processing wire early and working in different processes.
In order to meet the increasing order demand of customers, GCPB series backpack cabinet production line has been improved in one stream production mode operation for many times, one stream production mode operation of general assembly line; one stream production mode operation of bottom board wiring plus general assembly line; one stream production mode operation of controller wiring of heater control box, bottom board wiring plus general assembly production. The backpack cabinet production line not only has a daily delivery capacity of 100 sets, but can flexibly switch to produce more than 10 batch products of various types, such as heater control cabinet. Because the action decomposition and standardized operation, the operation difficulty is reduced and the product quality is effectively guaranteed.
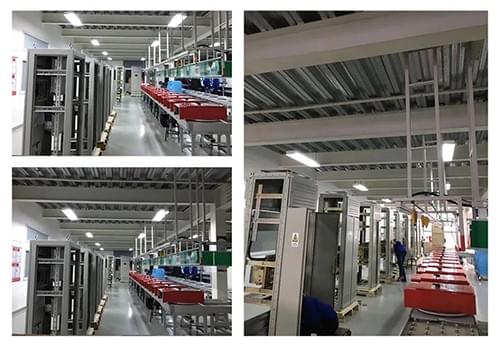
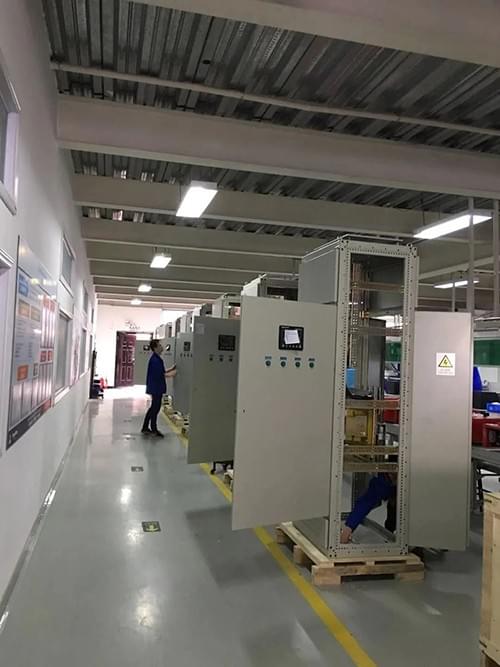
HWP series large heater production line is being tested and simulated to run one stream production mode and can provide data and scheme feasibility for the transformation of automatic production line. Currently the control box is produced separately and the daily delivery capacity of large heaters has reached 50 sets.
Every production line transformation, all station improvements, pieces of SOP writing, each careful communication, groups of wire installation, steel pipe construction one by one, cooperation and operation over and over again, every bit of advice, clap and praise every time......
A workshop with the spirit of unity, technical leadership and continuous improvement is in full swing.
Looking back is to make great strides forward.
Let’s work together, let’s inspire each other, and strive forward with full energy. The history of electronic control workshop will leave the footprints of our youth!
www.smartgen.cn
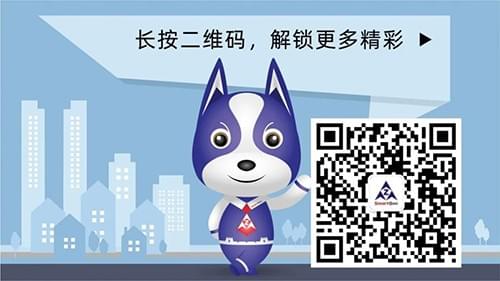